In construction projects that rely on dredging operations, connecting dredge pipelines is a crucial step that ensures materials like sediment and slurry are transported efficiently from dredging sites to designated locations. The effectiveness of connecting dredge pipelines directly influences the overall project timeline, safety measures, and environmental impact. A well-executed connection can minimize risks, while poor connections may lead to costly delays, environmental hazards, and safety concerns. This article focuses on the best practices for dredge pipelines, covering the most effective pipeline connection techniques and the essential construction pipeline connection tools to ensure secure and efficient operations.
Importance of Secure Dredge Pipeline Connections
The role of connecting dredge pipelines must be balanced in large-scale construction projects such as land reclamation, sediment removal, and marine construction. These pipelines transport a mixture of materials, including water and sediment, over vast distances, and their connections need to be strong, leak-proof, and reliable.
If the process of connecting dredge pipelines is done poorly, there can be frequent system failures, which can lead to major downtimes, unanticipated repair costs, and even safety incidents. Furthermore, compromised connections may lead to hazardous material spills that affect local ecosystems. By following the best practices for dredge pipelines, teams can ensure that the pipeline connections remain durable and functional throughout the project, reducing the chances of leaks and minimizing operational interruptions.
Common Pipeline Connection Techniques in Construction
The methods used for connecting dredge pipelines vary depending on the project’s requirements, materials, and environmental conditions. Some traditional and modern pipeline connection techniques are more suited to specific needs, so choosing the right method is essential for success. Let’s explore the three most common techniques used in construction:
Mechanical Coupling Methods
Mechanical coupling is one of the most widely used methods for connecting dredge pipelines. This method uses metal clamps to connect two pipe ends together securely. The benefit of this method is that it is quick to install and allows for easy assembly and disassembly, making it ideal for temporary projects where the pipeline will be moved or adjusted frequently.
However, mechanical couplings can experience wear and tear, especially in harsh environmental conditions, such as exposure to saltwater or abrasive materials. For this reason, regular inspection and maintenance are necessary to ensure that mechanical couplings remain effective throughout the project.
Flanged Connections
Flanged connections are another common method for connecting dredge pipelines. In this technique, two pipe sections are bolted together using metal flanges to create a secure, leak-proof seal. Flanged connections are typically used in long-term projects where a more permanent and reliable pipeline is needed. They are preferred for high-pressure applications because they are durable and resistant to pressure loss.
However, flanged connections require more labor during installation, as it is essential to properly align the flanges and torque the bolts to the correct specifications. The use of hydraulic torque tools is often necessary to ensure a secure and durable seal.
HDPE Fusion Welding
High-density Polyethylene (HDPE) fusion welding is a modern technique for connecting dredge pipelines made from plastic. This method involves heating the ends of the pipes and fusing them, creating a seamless and leak-proof connection. HDPE fusion welding is especially beneficial for projects located in environmentally sensitive areas because it minimizes the risk of leaks.
Although HDPE fusion welding requires specialized equipment and skilled operators, it provides a long-lasting, high-quality connection. The up-front costs of this method may be higher than others, but the durability and reduced maintenance needs make it a popular choice for large-scale construction projects.
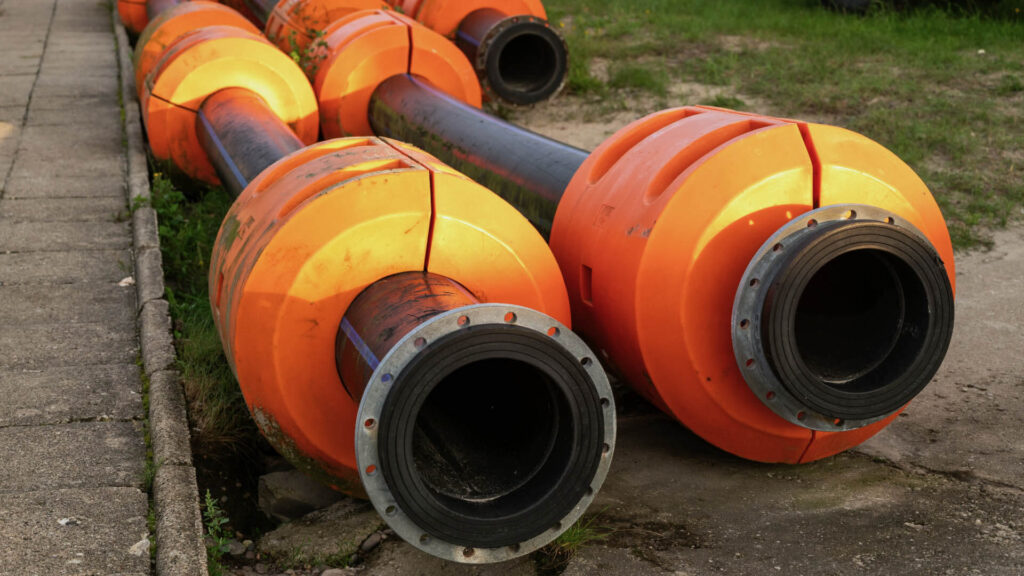
Essential Construction Pipeline Connection Tools
When connecting dredge pipelines, using the right construction pipeline connection tools is essential to achieving secure and long-lasting connections. These tools help ensure that the connections are made correctly, reducing the risk of system failures, leaks, and breakdowns. Here are some of the key tools used in pipeline connections:
Pipe Welding Machines
Pipe welding machines are crucial for HDPE fusion welding, allowing the pipes to be heated and fused seamlessly. These machines automate much of the process, making them a reliable option for ensuring strong and leak-proof connections. For teams using fusion welding as their primary method for connecting dredge pipelines, investing in high-quality pipe welding machines can significantly reduce installation time and improve the overall strength of the pipeline.
Hydraulic Torque Tools and Bolt Tensioners
For flanged connections, hydraulic torque tools and bolt tensioners are indispensable. These tools ensure that bolts are tightened evenly and to the correct torque, which is essential for creating a secure and leak-proof connection. Improperly tensioned bolts can result in leaks or pressure loss, leading to operational inefficiencies. Using hydraulic tools for connecting dredge pipelines ensures that the flanges are secured properly, minimizing the risk of system failure.
Dredge Pipe Clamps and Sealing Systems
Mechanical couplings rely on clamps and sealing systems to ensure that the pipes remain securely fastened. High-quality clamps can withstand high pressures and abrasive conditions, making them ideal for dredging projects where durability is key. Properly maintained sealing systems also help prevent leaks, ensuring that the mechanical couplings perform optimally throughout the project.
Using the right construction pipeline connection tools significantly improves the quality and longevity of the pipeline, ensuring that projects can proceed smoothly without costly interruptions.
Best Practices for Connecting Dredge Pipelines
To achieve the most secure and efficient pipeline connections, teams must follow the best practices for dredge pipelines. Implementing these practices will help ensure that the connections remain reliable, minimizing downtime and extending the life of the pipeline:
Regular Inspection and Preventive Maintenance
One of the most critical best practices is conducting regular inspections and preventive maintenance. Over time, even the most secure pipeline connections can experience wear and tear. Regularly checking for loose bolts, degraded clamps, or signs of wear helps teams identify potential issues early, preventing larger problems down the line.
Proper Alignment and Tensioning During Installation
When connecting dredge pipelines, ensuring proper alignment and tensioning during the installation process is crucial. Misaligned pipes can lead to undue stress, which may result in cracks, leaks, or even full system failure. For flanged connections, evenly tightening the bolts ensures that the seal is secure, preventing leaks and pressure loss.
Using Appropriate Tools for Specific Connection Types
Different pipeline connection techniques require different tools for successful installation. Whether it’s using pipe welding machines for HDPE fusion welding or hydraulic torque tools for flanged connections, using the right construction pipeline connection tools ensures that the connections are made correctly and securely.
Environmental Considerations
In environmentally sensitive areas, additional precautions must be taken to avoid damaging ecosystems. Methods such as HDPE fusion welding, which creates seamless and leak-free connections, are often the best choice. Using corrosion-resistant materials and conducting regular inspections further minimizes the risk of leaks and environmental contamination.
Common Challenges and Solutions in Dredge Pipeline Connections
Despite careful planning and installation, challenges may still arise when connecting dredge pipelines. Common issues include misalignment, leaks, and pressure loss. Misalignment can be avoided by ensuring precise measurements and using proper alignment tools during installation. Leaks can be mitigated by regularly inspecting mechanical couplings and replacing worn-out seals. Pressure loss can be minimized by using the correct torque during flanged connection installation.
By adhering to these solutions and using the appropriate pipeline connection techniques, teams can prevent major issues and ensure that their dredge pipelines remain secure and functional.
Conclusion
Successfully connecting dredge pipelines is critical for the efficiency, safety, and environmental sustainability of construction projects involving dredging operations. By following the best practices for dredge pipelines, using the correct pipeline connection techniques, and investing in high-quality construction pipeline connection tools, teams can reduce the risk of operational failures and enhance the overall performance of their projects. Properly connected dredge pipelines lead to more reliable and efficient dredging operations, minimizing downtime and ensuring project success.