Industrial pumping systems play a crucial role in mining operations, ensuring the efficient movement of water, slurry, chemicals, and other materials essential to the extraction and processing of minerals. In a sector known for its challenging environments, mining industrial pumps must not only be reliable but also highly efficient to minimize operational costs and downtime. Mining companies depend on these systems to transport abrasive materials, manage dewatering, and handle hazardous chemicals safely.
The key to a successful pumping system in mining is balancing reliability and efficiency with rugged conditions, including abrasive materials and extreme pressure variations; mining industrial pumps need to operate flawlessly while conserving energy. In this article, we’ll explore different types of industrial pumping systems used in mining, the features that make them reliable, and the ways modern technologies are enhancing their efficiency.
2. Types of Industrial Pumping Systems Used in Mining
There are several types of mining industrial pumps that mining operations rely on, each designed to meet specific needs depending on the material being moved and the environment in which they operate.
Centrifugal Pumps
Centrifugal pumps are one of the most commonly used pumps in mining operations due to their versatility. These pumps work by converting rotational kinetic energy into hydrodynamic energy to move fluids, making them highly effective for transporting water and low-viscosity liquids. In mining, centrifugal pumps are frequently used for tasks such as dewatering, water circulation, and transporting slurry.
The primary advantage of centrifugal pumps is their simple design and ease of maintenance. They are cost-effective and ideal for moving large volumes of fluid. However, they are less suitable for transporting thick slurries or highly abrasive materials, as these can wear down internal components over time, reducing efficiency and necessitating frequent maintenance.
Positive Displacement Pumps
Positive displacement pumps are a crucial part of mining industrial pumps, especially when dealing with thick slurries and abrasive materials. Unlike centrifugal pumps, which rely on kinetic energy, positive displacement pumps trap a fixed amount of fluid and push it through the system, making them ideal for high-viscosity fluids. These pumps, including diaphragm, piston, and peristaltic types, are also commonly used as chemical handling pumps, ensuring the safe transport of corrosive or hazardous fluids in mining operations.
Diaphragm pumps are well-suited for pumping abrasive slurries, while peristaltic pumps excel at handling chemical handling pumps. Positive displacement pumps are highly effective in handling concentrated slurries and other demanding materials, making them invaluable in mining operations where efficiency and the ability to manage harsh substances are critical.
Submersible Pumps
Submersible pumps are an essential component of mining industrial pumps, particularly for underground mining operations where dewatering is critical. These pumps operate while fully submerged in the fluid they are pumping, allowing them to efficiently remove water and slurry from flooded areas, mining pits, and groundwater sources. Because submersible pumps are positioned directly in the fluid, they are protected from external damage, making them highly durable and reliable in the rough conditions typically found in mining environments.
One of the key advantages of submersible pumps is their ability to operate quietly and efficiently. They ensure that mining operations can continue without interruption from groundwater intrusion, preventing delays and allowing for safe extraction.
Chemical Pumping Systems
Chemical handling pumps are a critical component of mining industrial pumps, specifically designed to manage hazardous materials commonly found in mining operations. These pumps must meet stringent safety and durability standards to ensure that toxic or corrosive chemicals are transported without leaks or spills. Special features such as double seals and corrosion-resistant materials are often incorporated into these chemical handling pumps to safeguard both workers and the environment, making them essential for maintaining safety and regulatory compliance in mining operations.
3. Key Features of Reliable Industrial Pumping Systems
Mining environments are tough, and mining industrial pumps need to withstand extreme conditions while operating efficiently. Several key features contribute to the reliability and performance of efficient pumping systems in mining.
Durability in Harsh Environments
Mining industrial pumps must be constructed from materials that can handle abrasive slurries and extreme conditions. Hard-wearing materials, such as high-grade steel and specialized coatings, are often used to protect pump components from premature wear and tear. This durability is key to maintaining efficient pumping systems, ensuring the pumps can operate reliably for long periods and reducing the frequency of repairs and replacements.
Energy Efficiency
With mining being an energy-intensive industry, optimizing energy use in efficient pumping systems is a top priority. Variable Frequency Drives (VFDs) are often incorporated into mining industrial pumps to adjust the motor speed based on the flow rate needed. By modulating the pump’s energy consumption in real-time, VFDs help ensure efficient pumping systems by minimizing energy wastage and lowering operational costs.
Minimal Downtime
Regular maintenance is key to keeping mining industrial pumps running efficiently. Many modern, efficient pumping systems are equipped with real-time monitoring technologies that track performance metrics such as flow rate, pressure, and energy consumption. By identifying potential issues before they cause breakdowns, operators can schedule maintenance proactively, reducing costly downtime and ensuring continuous operation of these efficient pumping systems.
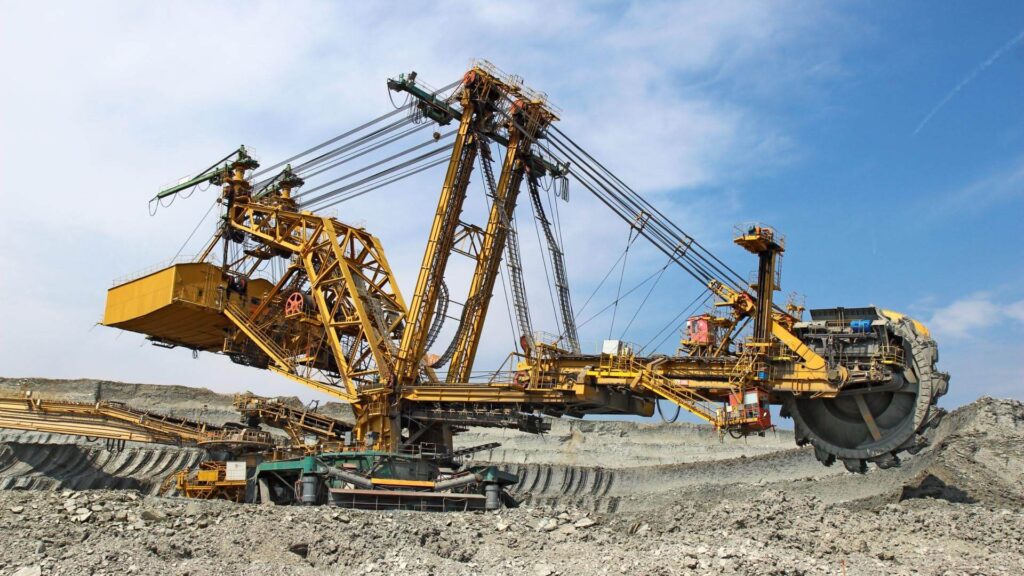
4. Enhancing Operational Efficiency with Modern Pumping Systems
Advances in technology have significantly improved the performance and efficiency of mining industrial pumps.
Automation and Smart Monitoring
Automation has become a game-changer in mining pump operations. By integrating pumps with the Internet of Things (IoT) and automated controls, mining companies can remotely monitor and adjust their pumping systems in real-time. This level of control enables operators to respond instantly to changing conditions, improving pump performance and reducing the risk of mechanical failures.
Advanced Sealing and Wear-Resistant Materials
One of the biggest challenges for mining industrial pumps is handling abrasive materials. Advances in sealing technologies and the development of wear-resistant materials have greatly improved the longevity of pumps. These innovations help reduce the need for frequent maintenance and extend the life of efficient pumping systems, ensuring they remain operational even in the harshest mining environments.
5. Safety Considerations for Mining Pumping Systems
Safety is paramount in mining, and mining industrial pumps must be equipped with the necessary features to protect both workers and the environment.
Overpressure Protection and Safety Alarms
Mining pumps must be designed to prevent overpressure, which can lead to catastrophic equipment failure. Overpressure protection devices, such as pressure relief valves and safety alarms, are critical components that monitor the system and release pressure when necessary to prevent accidents.
Handling Toxic and Abrasive Materials Safely
Many mining operations involve the transportation of toxic chemicals and abrasive slurries. Pumps designed for chemical handling pumps are equipped with double-seal mechanisms and corrosion-resistant materials to prevent leaks, spills, and contamination. These safety measures are essential for protecting workers and maintaining compliance with environmental regulations.
6. Conclusion
Industrial pumping systems, particularly mining industrial pumps, are the backbone of modern mining operations, ensuring the reliable and efficient transport of water, slurry, and hazardous chemicals. Choosing the right pump for specific tasks, whether it’s centrifugal, positive displacement, submersible, or chemical handling pumps, is essential for maximizing operational efficiency and safety. These efficient pumping systems play a pivotal role in meeting the demanding requirements of mining environments while maintaining productivity and protecting workers and the environment.
By focusing on durability, energy efficiency, and minimal downtime, mining companies can ensure that their efficient pumping systems operate effectively even in the harshest environments. Looking ahead, the integration of smart monitoring technologies, wear-resistant materials, and automation will continue to enhance the performance of mining industrial pumps, driving further improvements in reliability and efficiency.
Mining companies that invest in advanced pumping systems will not only improve their bottom line but also ensure safer, more sustainable operations.