Handling abrasive slurries is one of the toughest challenges in industrial environments. Applications such as mining, tunneling, dredging, and wastewater management often involve fluids with high concentrations of solids, sharp particles, and corrosive elements. These harsh conditions can rapidly degrade standard pumps, leading to frequent breakdowns, costly maintenance, and lost productivity.
To maintain performance and minimize downtime, there is a growing demand for reliable, high-efficiency pumping systems designed specifically for these environments. This is where submersible slurry pumps have become increasingly popular. These pumps operate directly in the slurry, eliminating the need for extensive suction piping and priming systems. Their fully submerged design provides stronger suction, improved flow efficiency, and better solids handling, making them a practical solution for abrasive slurry transfer.
An industrial submersible pump is built with heavy-duty materials and components to withstand constant exposure to abrasive and corrosive materials. It offers rugged performance while reducing the complexity of installation and operation. For the most extreme conditions, a heavy-duty submersible slurry pump provides the durability and power needed for high-volume, high-density slurry movement.
This blog explores why submersible slurry pumps are the preferred choice for handling abrasive slurries and how selecting the right industrial submersible pump can improve efficiency and reduce operational costs.
What Are Submersible Slurry Pumps?
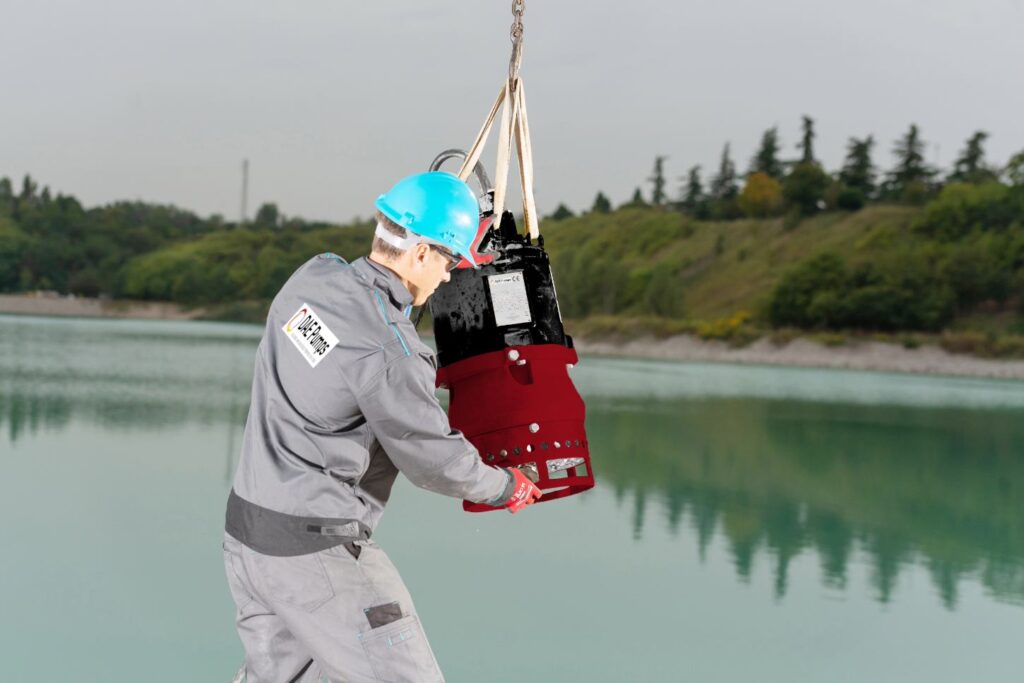
A. Definition and Operating Principle
Submersible slurry pumps are a specialized class of pumping equipment designed to operate while fully submerged in the fluid they are moving. Unlike surface pumps, which rely on suction and external piping, these pumps work directly within the slurry. This design eliminates many common issues associated with traditional pumping systems, such as air locking, priming delays, and suction limitations.
One of the main advantages of submersible slurry pumps is their ability to provide consistent and powerful fluid movement, even in high-solid, abrasive conditions. Being submerged allows these pumps to generate immediate hydraulic pressure at the source, reducing energy loss and improving efficiency. Their compact, all-in-one configuration also simplifies installation, making them ideal for confined spaces, deep pits, and remote sites.
B. Key Components of a Submersible Slurry Pump
At the heart of every high-performing unit are several key components engineered for demanding industrial environments. The impeller is specifically designed for solids handling, allowing the pump to move thick, abrasive slurries without clogging. Many impellers in heavy-duty submersible slurry pump models are open or semi-open in design to accommodate larger particle sizes and reduce wear.
The motor and seals are equally critical. A true industrial submersible pump will feature a fully enclosed, water-tight motor housing and mechanical seal systems built to resist abrasive infiltration. These components ensure long-term reliability even under continuous operation.
Another defining characteristic of submersible slurry pumps is their use of corrosion- and abrasion-resistant materials. Casings, wear plates, and impellers are often made from high-chrome alloys, hardened steel, or rubber-lined parts to prolong service life and minimize maintenance.
Whether in mining, construction, or dredging applications, the combination of durability, solids-handling capabilities, and ease of use makes submersible slurry pumps the preferred solution. When selecting an industrial submersible pump for tough environments, opting for a heavy-duty submersible slurry pump ensures maximum uptime and efficient performance under extreme conditions.
Common Challenges of Pumping Abrasive Slurries
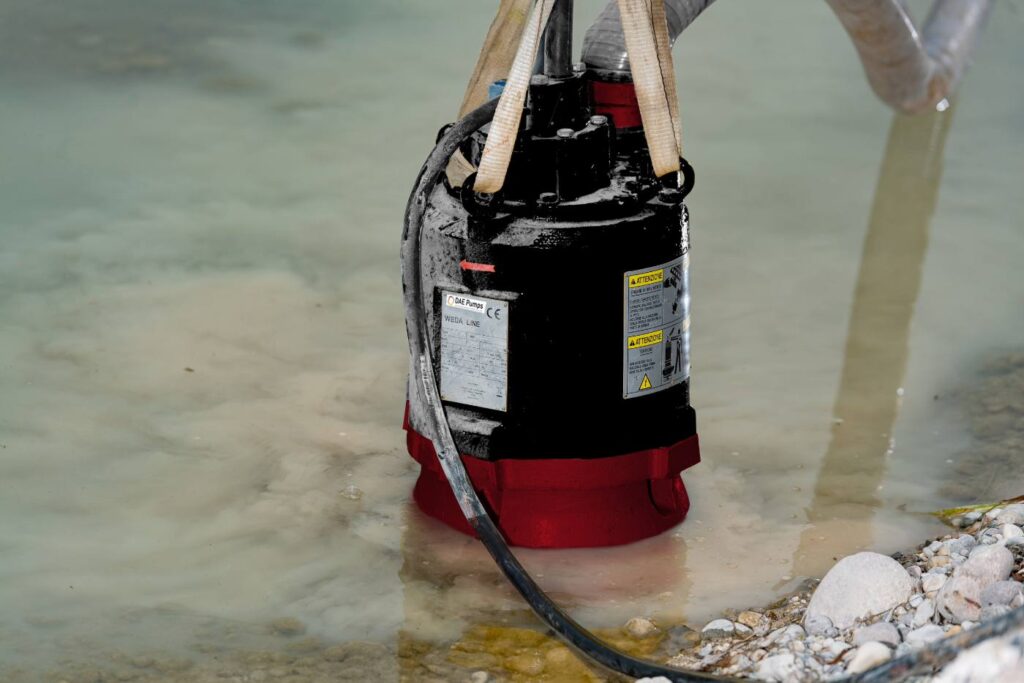
Abrasive slurries are notoriously difficult to handle due to their high solid content, coarse particles, and often corrosive chemical makeup. Industries like mining, construction, and dredging frequently encounter these materials, which can quickly wear down equipment and lead to performance issues. Traditional pumping systems often struggle in these environments, resulting in excessive downtime, rising maintenance costs, and reduced productivity.
One of the most significant challenges is the high rate of wear on internal components. Impellers, casings, and seals in standard pumps are not designed to handle continuous exposure to sharp, abrasive particles. This leads to accelerated degradation, frequent part replacements, and unplanned outages. In contrast, submersible slurry pumps are engineered to operate directly within abrasive slurries, using wear-resistant materials and specialized designs to extend lifespan and maintain performance.
Frequent clogging is another major concern. Conventional pumps often become blocked when handling slurries with large or irregularly shaped solids, requiring constant cleaning and maintenance. Submersible slurry pumps, especially those equipped with vortex or open-style impellers, are better suited to passing solids without obstruction, reducing the need for operator intervention.
Traditional pumps also fall short when it comes to efficient solids handling. Surface-mounted systems lose suction power over distance and may require additional infrastructure like priming chambers and slurry agitation systems to operate effectively. On the other hand, an industrial submersible pump is fully immersed in the fluid, enabling direct suction and reducing energy loss. This improves throughput and reduces operating costs over time.
Finally, all these issues contribute to costly downtime. When pumps fail or require frequent servicing, operations are delayed, and output declines. Investing in a heavy-duty submersible slurry pump addresses these concerns head-on. With rugged construction, efficient solids handling, and minimal maintenance requirements, an industrial submersible pump provides a dependable solution for the toughest slurry applications.
By overcoming these common challenges, submersible slurry pumps help operators achieve higher uptime, longer service life, and better return on investment.
Why Submersible Slurry Pumps Excel in Abrasive Conditions
Submersible slurry pumps are purpose-built to outperform traditional pump types in environments where abrasive slurries are the norm. Their unique design allows them to operate while fully submerged in the fluid, giving them key performance advantages in the most demanding applications.
A. Direct Fluid Contact and Efficient Pumping
One of the standout benefits of submersible slurry pumps is their direct immersion in the slurry itself. This setup eliminates the need for suction lift, which can be a major source of energy loss and inefficiency in surface-mounted pumps. By sitting directly in the slurry, these pumps create stronger suction, handle denser materials more effectively, and significantly reduce the risk of air-locking or cavitation. The result is consistent, efficient pumping without the need for extensive priming systems.
B. Minimal Infrastructure and Easy Deployment
Submersible slurry pumps require less infrastructure than their surface counterparts. There’s no need for suction lines, priming chambers, or elaborate mounting platforms. This ease of deployment makes them ideal for use in pits, tanks, sumps, tailings ponds, and flooded construction sites—essentially anywhere you need immediate and reliable slurry removal. Their compact design also makes them suitable for tight or remote spaces where setup time and space are limited.
C. Robust Construction for Harsh Environments
A major reason why these pumps excel in abrasive conditions is their durability. An industrial submersible pump is built with corrosion- and abrasion-resistant materials such as high-chrome alloys or hardened steel. These pumps often include features like heavy-duty mechanical seals, reinforced impellers, and moisture detection systems to extend service life and reduce failure risks.
In the most extreme conditions, a heavy-duty submersible slurry pump offers enhanced protection and performance. These models are designed to withstand constant exposure to highly abrasive, high-solid content slurries without compromising on flow rate or efficiency. Whether in mining, tunneling, or dredging, using a heavy-duty submersible slurry pump ensures long-term reliability and operational success.
In all these aspects, submersible slurry pumps provide a rugged, efficient, and low-maintenance solution for abrasive slurry handling that outperforms traditional alternatives.
Key Applications of Industrial Submersible Pumps
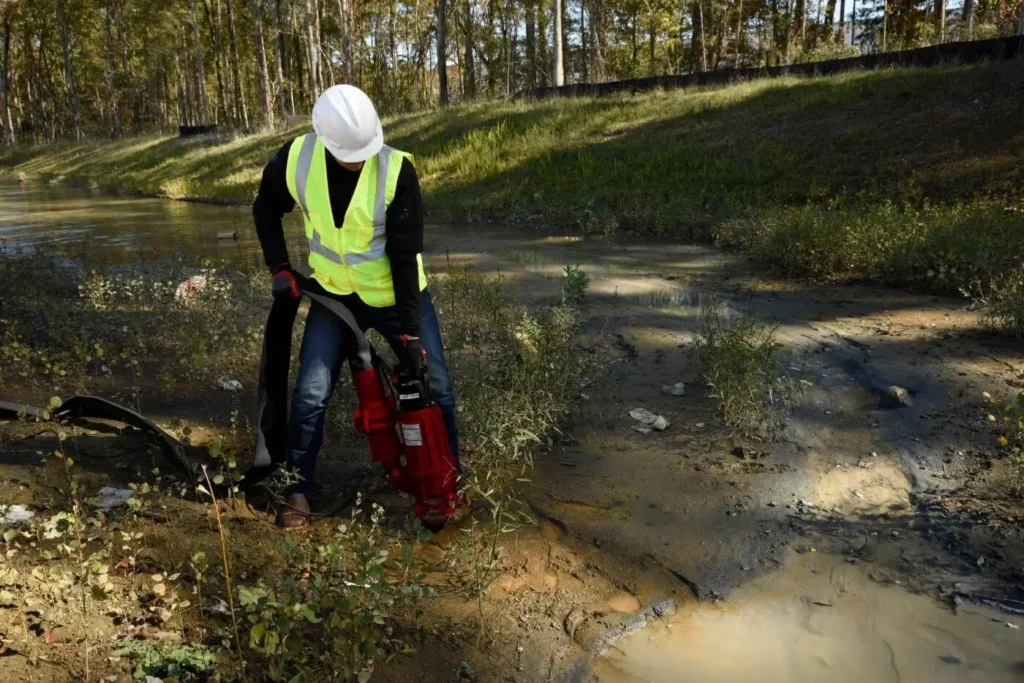
Submersible slurry pumps are widely used across a variety of industries due to their unmatched ability to handle abrasive, high-solid content fluids in challenging environments. Their submersible design makes them an ideal fit for operations where efficient solids handling, minimal infrastructure, and reliable performance are essential.
Mining: Tailings Ponds, Dewatering, and Slurry Transport
In the mining industry, managing slurry is a constant challenge. From dewatering deep mine shafts to transporting tailings and mineral-rich slurries, the need for durable, low-maintenance pumping systems is critical. Submersible slurry pumps can be deployed directly into tailings ponds or collection pits, where they efficiently handle dense and abrasive mixtures without requiring suction lines or external priming. Using a heavy-duty submersible slurry pump ensures consistent operation, even in remote or highly corrosive environments.
Dredging: Underwater Sediment Removal
Dredging projects often involve removing accumulated sediments from rivers, harbors, canals, and reservoirs. These tasks require pumps capable of operating underwater while handling sand, silt, gravel, and debris. Submersible slurry pumps are perfect for this application due to their submerged operation, which enhances suction and prevents clogging. Their rugged build makes them highly resistant to wear, and an industrial submersible pump can run continuously for long dredging campaigns with minimal maintenance.
Construction: Excavation Site Drainage
On construction sites, especially those involving deep excavation or foundation work, controlling groundwater and removing slurry is essential for maintaining safety and schedule. Industrial submersible pump systems offer a compact, mobile, and reliable solution for these scenarios. A heavy-duty submersible slurry pump can manage everything from water mixed with bentonite or concrete waste to compacted sludge, providing reliable drainage with reduced manual intervention.
Wastewater and Industrial Sludge Management
In wastewater treatment and industrial processing plants, submersible slurry pumps are critical for handling thick sludge, grit, and suspended solids. Their sealed motors, abrasion-resistant components, and ability to operate submerged make them ideal for long-term operation in corrosive and contaminated environments.
In all these applications, submersible slurry pumps stand out for their performance, reliability, and adaptability, making them indispensable across heavy-duty industrial sectors.
Features to Look for in a Heavy-Duty Submersible Slurry Pump
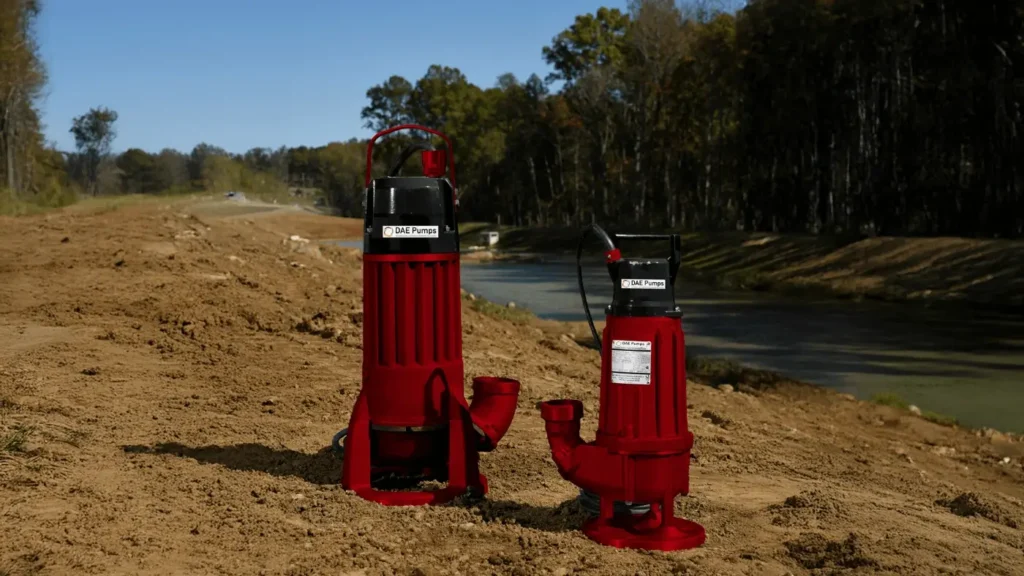
When selecting a pump for abrasive and high-solid content applications, it’s essential to evaluate key features that directly impact performance, longevity, and operational efficiency. The best heavy-duty submersible slurry pump models are built to thrive in the harshest environments, offering dependable operation even under continuous stress.
Solids-handling capacity is one of the most critical considerations. A quality heavy-duty submersible slurry pump should be able to pass large solids without clogging or losing efficiency. Pumps with open or vortex-style impellers are especially effective in managing slurries with irregular particle sizes.
Motor power and efficiency are equally important. An industrial submersible pump should provide sufficient horsepower to meet the system’s flow and head requirements while maintaining energy efficiency. Built-in motor protection, including thermal overload protection, ensures safe operation under demanding conditions.
Durability depends on the use of wear-resistant materials. The most rugged submersible slurry pumps are constructed from high-chrome alloys, stainless steel, or elastomer-lined components to withstand constant abrasion and corrosion.
Seal design is another major factor. Double mechanical seals with oil-filled chambers provide maximum protection against slurry ingress, helping to extend pump life and reduce maintenance. A true heavy-duty submersible slurry pump will also include advanced sealing systems to prevent moisture intrusion into the motor housing.
Lastly, look for thermal overload and moisture detection features. These sensors are standard in high-quality industrial submersible pump models and serve as early warning systems, helping prevent motor failure and reducing unexpected downtime.
In demanding applications, cutting corners can lead to costly failures. By choosing submersible slurry pumps with these essential features, operators ensure long-term reliability, reduced maintenance, and optimal performance in the toughest conditions.
Conclusion
When it comes to handling abrasive slurries in mining, construction, dredging, or wastewater applications, few solutions offer the same level of performance and resilience as submersible slurry pumps. Their ability to operate while fully submerged provides significant advantages in terms of suction efficiency, solids handling, and ease of deployment, especially in harsh and space-constrained environments.
An industrial submersible pump is specifically engineered to endure high-solid content fluids, corrosive conditions, and extended operating hours without compromising performance. With features such as wear-resistant materials, advanced seal systems, and built-in motor protection, these pumps deliver both durability and long-term cost savings.
For the most demanding applications, a heavy-duty submersible slurry pump offers the rugged construction and high power needed to keep operations running smoothly, even in the toughest slurry environments.
In short, submersible slurry pumps stand out as the preferred solution for abrasive slurry handling, providing reliable, efficient, and low-maintenance performance that meets the demands of modern industrial operations.