Slurry pumps are essential in mining operations, where they transport abrasive and dense slurries, such as tailings and sludge, through pipelines. These pumps are designed to handle high-solids content, offering the durability and performance necessary to ensure smooth and efficient mining processes. When selecting a slurry pump for mining, it’s crucial to choose one that can handle the specific challenges of the operation, ensuring reliable and continuous performance.
Selecting the right mining slurry pump is crucial for maximizing efficiency and reducing operational costs. A well-chosen pump minimizes downtime, lowers energy consumption, and extends the pump’s lifespan, all of which contribute to improved cost-effectiveness over time. It’s important to work with reputable mining slurry pump manufacturers to ensure you are investing in a pump that meets the specific needs of your mining application.
This guide is intended for procurement heads, engineers, contractors, and decision-makers in the mining and heavy industries, providing valuable insights into the selection and sizing of slurry pumps for mining applications.
Understanding Mining Slurry Pumps
A mining slurry pump is a type of centrifugal pump specifically engineered to handle the demanding task of transporting slurries in mining operations. These slurries often consist of water mixed with solid particles such as sand, mud, tailings, or other mined materials. Unlike standard pumps, slurry pumps are designed with robust components that can withstand the high abrasiveness and corrosive nature of the materials being moved. Their specialized design allows them to effectively pump high-solids mixtures over long distances, which is crucial for various mining processes.
Mining slurry pumps are essential for applications that require the movement of mixtures with high concentrations of solids. These pumps offer the durability and reliability needed for continuous operation in tough mining environments, ensuring that material handling processes such as tailings disposal, mineral processing, and ore extraction can proceed efficiently without interruptions. Working with reputable mining slurry pump manufacturers ensures that the slurry pump for mining meets the specific needs of your operation, providing optimal performance and longevity in challenging conditions. Additionally, mining slurry pump manufacturers can offer customized solutions to further enhance the pump’s effectiveness in your unique mining applications.
Key Differences Between Slurry Pumps and Water Pumps
While both mining slurry pumps and water pumps are used to move liquids, there are key differences in their design and functionality:
- Handling of Solids: Water pumps are designed for clean water or low-solids fluids, while slurry pumps are built to handle thick, abrasive mixtures that contain large quantities of solid particles.
- Construction and Materials: Slurry pumps are constructed using materials like high-chrome alloys, rubber linings, or other wear-resistant materials to cope with the abrasive nature of slurries. Water pumps typically use less durable materials, as they are not exposed to the same harsh conditions.
- Clearance and Design Features: Slurry pumps have wider clearances in their components to allow for larger particles to pass through without clogging. In contrast, water pumps have tighter tolerances, making them ill-suited for handling solid materials.
These distinctions highlight why slurry pumps for mining are vital for mining operations, offering the durability and performance required for demanding tasks. By partnering with trusted mining slurry pump manufacturers, operators can ensure they select the right equipment to meet the specific challenges of their mining operations, providing reliable, long-term performance under harsh conditions.
Common Applications in Mining
Mining slurry pumps are used in several key applications across the industry, where the transport of dense, abrasive slurries is necessary. Some of the most common applications include:
- Pumping Abrasive, Dense Slurries: Mining slurry pumps are designed to handle dense mixtures like tailings, sludge, and sand, which can be challenging to move through pipelines. These pumps are engineered to minimize wear and maximize efficiency, even when transporting high-concentration solids.
- Mineral Processing: Mining slurry pumps play a vital role in mineral processing plants, where they are used to transport ore slurries during various stages of mineral extraction. These pumps ensure that minerals are separated efficiently, enabling smooth operations in flotation, gravity separation, and other processes.
- Coal Handling: In coal mining, slurry pumps are used to move coal slurry, a mixture of water and finely ground coal, during the washing and separation processes. These pumps are essential for maintaining the efficiency of coal processing and helping separate valuable coal from waste materials.
- Tailings Transport and Disposal: Mining slurry pumps are critical for the safe transport and disposal of tailings, which are the residual materials left after mineral extraction. These tailings are often highly abrasive and corrosive, necessitating durable and reliable slurry pumps to move them to storage or disposal sites.
By using the right slurry pump for mining, operations can benefit from improved process efficiency, reduced maintenance costs, and increased operational uptime. Leading mining slurry pump manufacturers offer pumps specifically designed to meet the unique demands of the mining industry, ensuring that projects are completed on time, within budget, and with optimal performance.
Key Factors to Consider When Choosing a Mining Slurry Pump
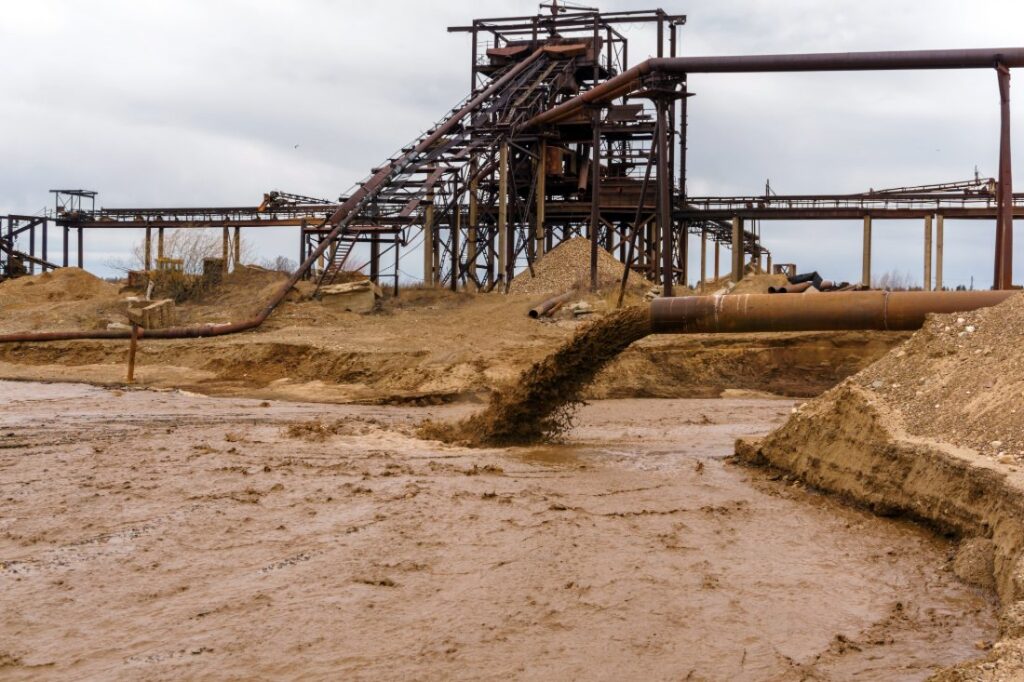
Slurry Characteristics
When selecting a slurry pump for mining, understanding the characteristics of the slurry to be pumped is crucial. The properties of the slurry, such as its abrasiveness, viscosity, and chemical composition, directly influence pump performance and durability. Working with trusted mining slurry pump manufacturers ensures that the selected pump is engineered to handle the specific demands of the slurry and provide reliable, long-lasting performance.
- Material to be Pumped: Mining slurries can be abrasive, viscous, or chemically aggressive. The material being transported affects the wear and tear on the pump components. For abrasive slurries like sand or mineral tailings, high-durability materials such as high-chrome steel or rubber linings are typically required to prevent excessive wear.
- Slurry Density and Viscosity: The density and viscosity of the slurry will impact the energy required to pump it. Denser slurries demand more powerful pumps, while more viscous slurries may require pumps with specialized features to maintain efficient flow. When selecting a slurry pump for mining, understanding these factors is key to ensuring optimal performance.
- Particle Size: The size and distribution of solid particles in the slurry are also important. Larger or irregularly shaped particles can increase wear and may necessitate pumps with larger clearances or those specifically designed for handling coarse slurries.
Pump Durability and Material Selection
Choosing a slurry pump for mining that can withstand the abrasive and corrosive nature of mining slurries is critical for maintaining reliable operation. The durability of the pump depends heavily on the materials used in its construction. Working with reputable mining slurry pump manufacturers ensures that the pump is built with high-quality, wear-resistant materials to meet the challenging conditions of mining environments.
- Material Selection: Pumps used in mining applications are typically made from wear-resistant materials such as high chrome iron, rubber, or duplex stainless steel. These materials are resistant to abrasion and corrosion, making them ideal for handling harsh slurry conditions. For example, high chrome iron is commonly used for its hardness and wear resistance, while rubber-lined pumps are effective in reducing wear when handling slurry with coarse solids.
- Corrosion and Wear Resistance: The slurry’s chemical composition, temperature, and abrasiveness influence the type of materials that should be selected for the pump. For slurries with aggressive chemicals or high corrosive potential, corrosion-resistant materials such as duplex stainless steel or specially coated components are essential to maintain pump integrity and extend its lifespan.
Slurry Concentration and Particle Size
The concentration of solids in a slurry can have a significant impact on pump performance. High solids concentrations increase the likelihood of pump wear, reduce pump efficiency, and may require a slurry pump for mining specifically designed to handle such conditions. Selecting the right pump from mining slurry pump manufacturers ensures that it is built to withstand the challenges posed by high-solids slurries, maintaining optimal performance and longevity.
- Handling Solids: Pumps that are designed to handle high solids concentrations are typically built with larger impellers, wide clearance areas, and reinforced materials to reduce clogging and wear. The larger the particle size, the more robust the pump must be to maintain a steady flow without compromising its operational efficiency.
Pump Performance Requirements
Flow Rate (Q)
The flow rate of a mining slurry pump is a critical parameter in ensuring that the required volume of slurry is transported efficiently through the system. To calculate the required flow rate, consider factors like the total volume of slurry to be pumped per unit of time, as well as the distance the slurry needs to be transported.
- How to Calculate Required Flow Rate: The flow rate is typically measured in cubic meters per hour (m³/h) or gallons per minute (GPM). To determine the required flow rate for your mining operation, assess the amount of slurry produced per day and the volume needed to be moved through the system. The pump should be capable of handling this flow without being undersized or oversized, which can lead to inefficiencies and unnecessary energy consumption.
- Effect of Flow Rate on Pump Size and Performance: The flow rate directly affects the size and performance of the pump. A pump that is too small will be unable to handle the required flow, leading to high energy consumption, overheating, and potential pump failure. Conversely, an oversized pump will consume more energy than necessary, reducing overall efficiency and increasing operating costs.
Head Requirements
Head refers to the energy required to move the slurry through the pump and piping system. The total dynamic head (TDH) is a key consideration when sizing a mining slurry pump, as it ensures that the pump can generate enough pressure to overcome the system’s resistance and deliver the slurry effectively.
- Defining Total Dynamic Head (TDH): TDH is the sum of three components:
- Static Head: The vertical distance between the slurry source and discharge point.
- Friction Head: The resistance caused by friction between the slurry and the walls of the pipe.
- Pressure Head: The pressure required to overcome any system or process pressure at the discharge point.
- Static Head: The vertical distance between the slurry source and discharge point.
- Sizing Pumps for the Required Head: A properly sized pump will need to generate enough pressure to overcome these resistance factors and maintain an efficient flow rate. When selecting a mining slurry pump, ensure that the pump’s head capacity aligns with the total dynamic head calculated for your specific application.
Performance Curves and Best Efficiency Point (BEP)
Understanding pump performance curves is essential for selecting the right slurry pump for your mining application. These curves provide a graphical representation of a pump’s performance at different flow rates and head conditions, helping to identify the optimal operating range.
- Explanation of Pump Performance Curves: A pump performance curve plots flow rate against head and shows the pump’s efficiency at various points. The curve allows operators to determine the best operating point for the pump, ensuring that it runs at maximum efficiency.
- Importance of Operating Near BEP for Longevity and Efficiency: The Best Efficiency Point (BEP) is the point on the performance curve where the pump operates most efficiently. Operating near the BEP ensures that the pump delivers the required flow and head while minimizing energy consumption, wear, and maintenance costs. Pumps that consistently operate far from the BEP tend to experience higher energy losses and faster wear, reducing their overall lifespan and increasing operational costs.
By carefully considering flow rate, head requirements, and the pump’s performance curve, you can ensure that the selected mining slurry pump is both cost-effective and efficient, delivering optimal results for your mining operation.
Sizing a Mining Slurry Pump
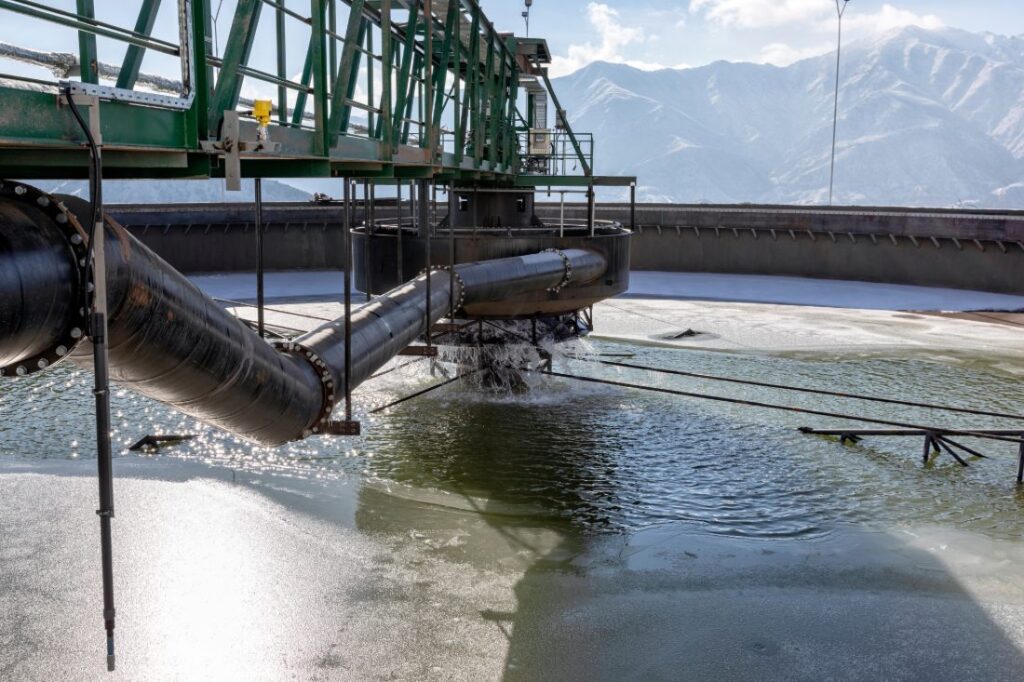
Step-by-Step Sizing Process
Sizing a mining slurry pump accurately is essential for ensuring optimal performance and energy efficiency in mining operations. The correct pump size helps prevent issues such as excessive wear, poor efficiency, and unnecessary downtime. The sizing process involves several key calculations that consider the slurry’s characteristics, as well as the operational requirements of the pump. By working with trusted mining slurry pump manufacturers, you can ensure that the selected slurry pump for mining is properly sized to meet the unique demands of your operation, delivering reliable performance while minimizing energy consumption and maintenance costs.
- How to Calculate Flow Rate, Static Head, and Friction Losses:
The first step in sizing a mining slurry pump is calculating the required flow rate. This is based on the volume of slurry that needs to be transported over a given period. Flow rate can be expressed in cubic meters per hour (m³/h) or gallons per minute (GPM), depending on your local units of measurement.
- Static Head: This refers to the vertical distance between the slurry source and the discharge point. It’s a crucial component for determining how much pressure the pump must generate to overcome gravity and lift the slurry.
- Friction Losses: As the slurry moves through the pipeline, friction between the slurry and the pipe walls reduces the flow efficiency. Friction losses depend on factors like pipe length, diameter, and roughness, as well as the flow rate and slurry characteristics.
- Static Head: This refers to the vertical distance between the slurry source and the discharge point. It’s a crucial component for determining how much pressure the pump must generate to overcome gravity and lift the slurry.
- Determining Total Dynamic Head (TDH) and the Correct Pump Size:
The next step is calculating the total dynamic head (TDH), which is the sum of the static head, friction head, and any additional pressure head required at the discharge point. The TDH calculation ensures that the pump can provide the necessary pressure to move the slurry through the entire system. Once the TDH is calculated, it can be used to select the appropriate pump size from the performance curves provided by mining slurry pump manufacturers.
Calculating Pump Power Requirements
The power required by a slurry pump is determined by the flow rate and the head that the pump must overcome. Correctly sizing the motor for your slurry pump for mining ensures that the pump operates efficiently without overloading or underperforming.
- Brake Horsepower (BHP) Calculation Formula and Its Significance in Selecting the Right Motor:
The brake horsepower (BHP) is a measure of the energy required to operate the pump. The formula for calculating BHP is as follows:
BHP=Q×h×Sp.Gr3960×Efficiency\text{BHP} = \frac{Q \times h \times \text{Sp.Gr}}{3960 \times \text{Efficiency}}BHP=3960×EfficiencyQ×h×Sp.Gr
Where:
- Q = Flow rate (in GPM)
- h = Head (in feet)
- Sp.Gr = Specific gravity of the slurry
- Efficiency = Pump efficiency (as a decimal)
- 3960 = A constant used to convert units to horsepower
- Q = Flow rate (in GPM)
- This calculation helps determine the horsepower needed to handle the slurry’s flow and pressure demands. It is essential to select a motor that provides enough power to meet these requirements without being oversized, as this can lead to inefficient operation.
- Importance of Motor Sizing in Slurry Pump Selection:
Proper motor sizing ensures that the pump can handle the calculated flow rate and head while operating efficiently. If the motor is undersized, it may struggle to maintain the desired performance, leading to overheating, energy inefficiencies, and potential pump failure. Conversely, an oversized motor may consume more energy than needed, leading to higher operational costs.
Selecting the Correct Pump Size
Choosing the right size for your mining slurry pump involves more than just matching the flow rate and head. The pump must also be capable of operating within its Best Efficiency Point (BEP), where it performs most effectively and consumes the least amount of energy.
- Ensuring Pump Size Matches the Required Flow and Head While Operating Near BEP:
When selecting the correct pump size, the goal is to ensure that the pump operates at or near the BEP, which is typically represented by the intersection of the system curve (flow vs. head) and the pump curve. Operating near BEP maximizes pump efficiency, reduces energy consumption, and minimizes wear on the pump components, extending its lifespan. - Impact of Choosing the Wrong Size: Energy Losses, Excessive Wear, and Operational Downtime:
Selecting the wrong pump size can have serious consequences. An undersized pump may struggle to meet the flow and head requirements, leading to frequent breakdowns, excessive energy consumption, and a shorter pump lifespan. On the other hand, an oversized pump will operate inefficiently, consuming more power than necessary and causing unnecessary wear on its parts. This not only increases operating costs but also leads to increased downtime for repairs and maintenance.
Ensuring that the right mining slurry pump is chosen is critical to the success of any mining operation. By carefully following these sizing steps, operators can select a slurry pump for mining that will optimize performance, reduce costs, and improve the overall efficiency of slurry transport systems. Working with experienced mining slurry pump manufacturers ensures that the selected pump is designed to meet the specific challenges of your operation, providing maximum reliability and efficiency in demanding environments.
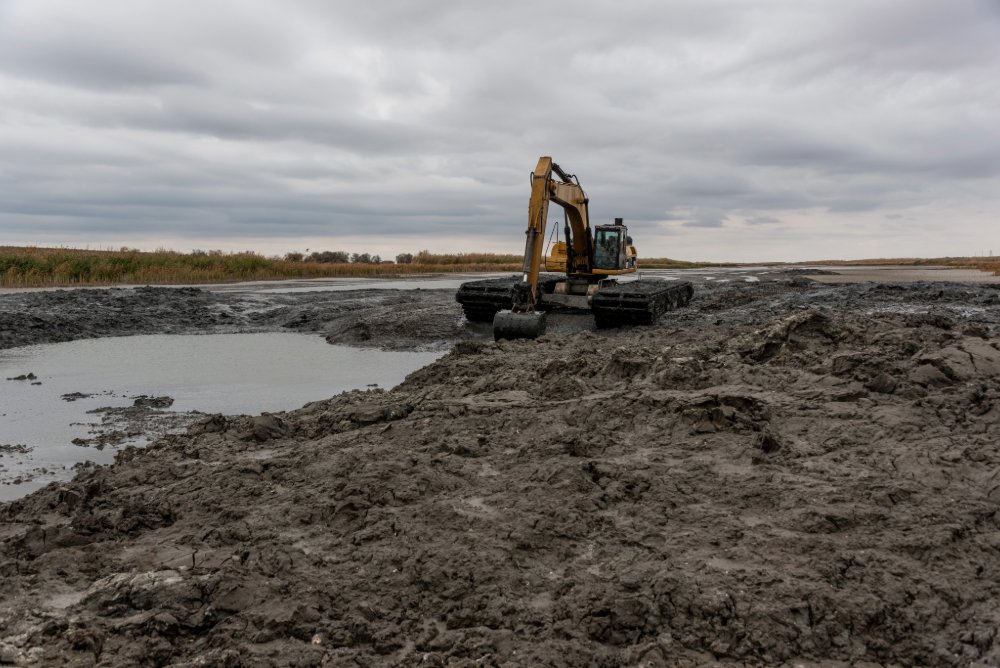
The Key to Successful Mining Slurry Pump Selection
Selecting the right mining slurry pump is essential for ensuring the efficient and cost-effective operation of mining processes. Key considerations include understanding the specific characteristics of the slurry, such as its density, viscosity, and particle size, as well as choosing materials that offer durability and corrosion resistance. Proper sizing, including flow rate, head requirements, and motor power, is crucial for maintaining performance and reducing operational costs.
Making an informed decision on the right slurry pump for mining can significantly enhance operational efficiency, minimize downtime, and extend the life of your equipment. A pump that is properly matched to the slurry’s properties and the operational demands will contribute to long-term success by optimizing energy use and reducing the frequency of costly repairs.For expert guidance in selecting the right mining slurry pump for your specific needs, we encourage you to contact our team. Explore the wide range of slurry pumps we offer and benefit from our years of experience in providing reliable, high-performance solutions for the mining industry. Let us help you make the best choice for your operation’s needs and ensure ongoing productivity and cost-efficiency.