Equipment
Flooded Suction Pumps
Highly Developed Pumps for the Easy Handling of Viscous and Abrasive Materials
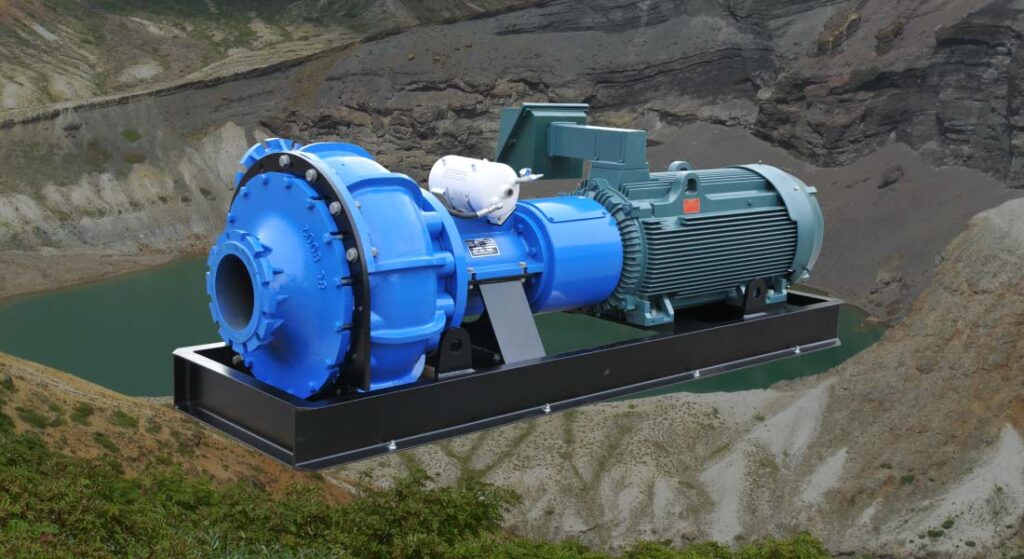
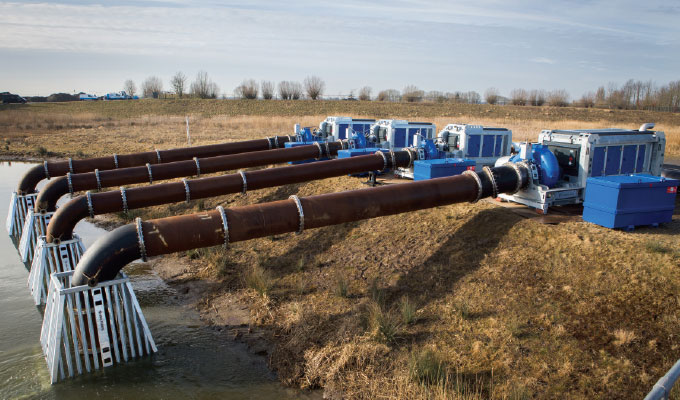
Some of the unique flooded suction industrial pumps include the horizontal–vertical flooded suction industrial pumps, which are designed for challenging pumping and dredging processes. Collectively, these pumps are ideal for pumping highly viscous and abrasive slurries, sludge, pastes, high solids material, and other difficult fluids, regardless of changing fluid levels.
Our pumps are built for endurance and dependability and are suitable for diverse industries and operations throughout the world. Perfect for high-viscosity product transfer or use in applications with challenging flow characteristics, our pumps are ready-made for your application environment.
Efficient and Affordable Pumping Technology
For challenging applications, Eddy Pump proves to be the most reliable pumping equipment. Its innovative design allows for the smooth pumping of abrasive and viscous substances without clogging. Furthermore, the minimal maintenance costs make it an economical long-term investment.
01
Exceptional Performance
Eddy Pump distinguishes it from the other pumps by its suitability for high flow applications and high pressure applications that are in most industries.
02
Innovative Anti-Clogging Design
Eddy Pump has been designed to avoid blockage despite the inclusion of large objects through its enhanced design. This, in a way, both improves the safety of the operation and makes it run more effectively.
03
Robust Resistance and Durability
Made from tough materials like high chrome alloys, the Eddy Pump units offer durability that is consistent and long-term based.
Flooded Suction Pumps: Precise, Gravity-driven Efficiency.
Flooded suction pumps are mostly used in sectors like wastewater treatment, mining, and construction industries and are most appropriate for difficult fluids and sludge. These pumps work with the help of placing the fluid higher than the inlet level to enable the fluid to flow in due to force of gravity.
This configuration also does not require pre-priming, making the operations continuous and sustainable by combining the natural forces with modern methods of engineering.
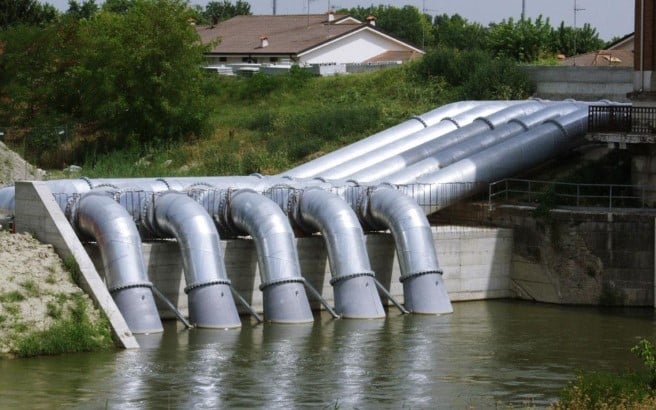
Horizontal Or Vertical Pumps: Which of the two should be chosen?
Deciding between horizontal and vertical slurry pumps involves considering several key factors, such as density, flow rate, pressure, the distance between the points, power source, temperature, pH, corrosion, and erosion. It is possible to choose a pump made of high-quality materials, which guarantees a longer duration of its functioning, so popular materials are presented in our list.
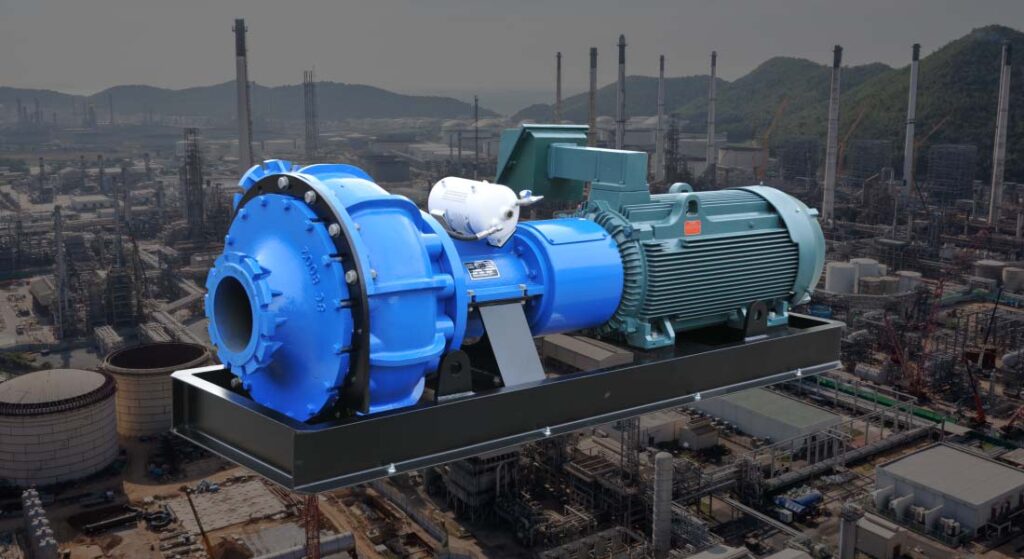
Horizontal Flooded Suction Pump
Ease of Installation and Maintenance: This simple design is has an added advantage in that it is easy to install, and at the same time the system does not require a lot of maintenance.
Increased Flow Rates: It has a relatively larger impeller to provide a high flow rate than other types of pumps.
Lower NPSH Requirements: It is also generally used where the Net Positive Suction Head is relatively lower compared to vertical pumps.
Larger Footprint: Takes up more space when compared to other types of furniture design.
Vertical Flooded Suction Pump
Compact Size: Due to its compact design, they can also be installed in cramped spaces or other harder-to-reach locations.
Highly Efficient: Particularly useful when the application of force requires a great deal of surface lift.
Versatile Design: Can be suspended by a cable and inserted into materials for pumping, which can increase the usage flexibility of the suction cup with fluid bar.
Maintenance Challenges: Repairs and maintenance are the activities, which, perhaps, are more challenging than any other designs.
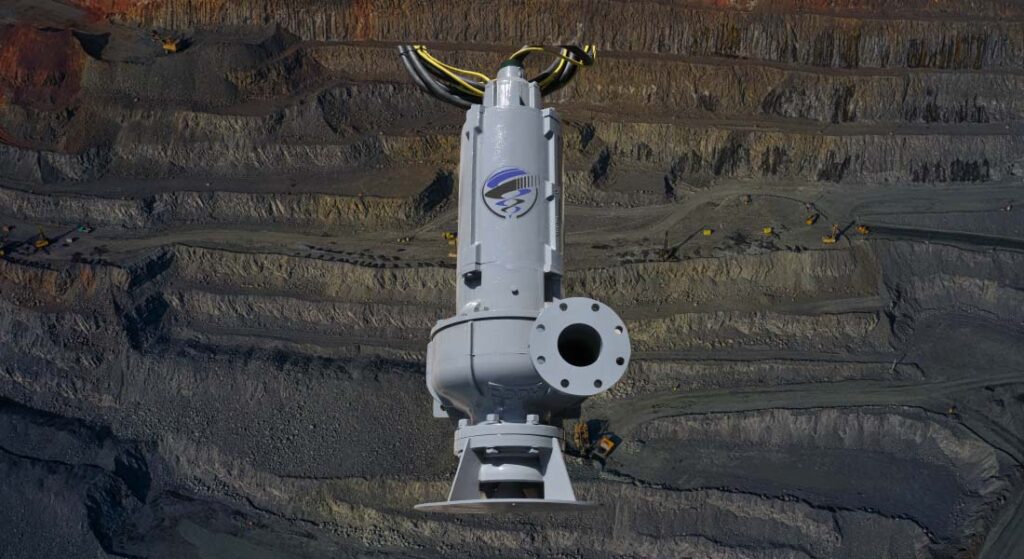
The semi-automated dredge requires 650 sq ft of floor space, has lower concentrations of energy, and can work with slightly elevated levels of water depth without employing onboard staff. Based on three or four cables, this system comes with an aspect of winches whereby it can be controlled by electronic instruments to enable easy ordering along the defined dredging route, pump depth control, and pump RPM. The Globestar’s patented cable deployment system allows the dredge to operate at working depths of 100 feet, and it has no internal structures, which means it can work 24 hours a day.
Consideration of the key parameters when choosing Stations of a pump
Manufacturers should thus direct more attention towards either designing or acquiring coalescing pumps that are suitable to be used under flooded suction. Specifically, the focus should be made on the reliable creation of structures that meet necessary standards and requirements for the effective handling of fluids and the provision of steady performance.
The flooded suction (Submersible pumps) is useful for pumping fluids with suspended solids content and high viscosity; it is referred to as Slurry. It transfers high viscosity liquids provided it is loaded with particles, debris or abrasive substances.
These pumps come with a screen that allows solids to pass through easily, thus experiencing less blockage hence, use lesser repair materials, and the costs are relatively cheaper.
Automated water intake requires a screen guard to minimize the effects of sediments accumulating on its walls and the subsequently reduced flow rate.
Made from strong materials and having powerful pumps installed, these types of units do not corrode easily and demonstrate high wear resistance, thus ensuring a long service duration.
Multi-stage high pressure pumps are used to make the directing of abrasive slurries and fluids economic. The flow rate managed by the pump requires being regulated to ensure it meets expectations for the fluid to be managed.
Increase this capability and guarantee that the pump is capable of achieving the designed head pressure which refers to the vertical height a pump has to lift the fluid.
As for the materials used in constructing the pump to ascertain whether it can transport the intended fluids, this has to be assessed. Materials used may differ depending on the use and type of fluid like the use of stainless steel utensils for corrosive liquids or HDPE utensils for oils.
Check the functionality of the pump motor. Some products may require pump with higher capacity and ability to move through heavier fluid circulation with ease.
Select pump types that have leakage resistant capabilities so that fluid loss is controlled and the pump can perform efficiently.
It will be wise to look at such aspects as transport, serviceability, and the overall support throughout the product’s life cycle as well as services and spare parts.
Some important qualities include Overload protection, thermal sensors, protective guards on the pump to enhance safety and to avoid severe loss of the equipment.
This is especially important because the market offers a range of pumps with varying design and quality, and therefore, one has to select pumps from manufacturers who are known to produce some of the best products in terms of design and durability.
Advantages of Varies Applications in Pump Technology
Solids Handling Capacity
These pumps are designed to handle fluids that contain high solid content or belong to slurry category, and are capable of operating on fluids that have particles, debris or abrasive substance in them.
Reduced Obstruction Risk
The design of these pumps enables solids to be pumped without blocking the passage of water through the pump, thereby reducing the need for repairs and maintenance.
Improved Efficiency
Submerged suction pumps make it easier to manage blockages and attain better through put rates thus increasing operation efficiency.
Enhanced Wear Resistance
Made of sturdy materials and having additionals that enhance the durability of the product, these specific pumps provide longer service time and wear resistance.
Cost-Effective Solution
Flooded suction pumps are very efficient and relatively cheaper to purchase which make them ideal especially when dealing with slurries and other difficult fluids making it an ideal fluid handling system at a fairly cheap cost.
Get to know our pump models
Model | Diameter | GPM Flow | Head |
HD1K | 1.5 x 1 Inch | 1 – 200 | up to 170 feet |
HD 2000 | 3 x 3 inches | 50 – 390 | up to 90 feet |
HH 2000 | 3 x 3 inches | 100 – 600 | up to 350 feet |
HD 3000 | 4 x 3 inches | 100 – 780 | up to 130 feet |
HD 4000 | 6 x 4 inches | 250 – 2100 | up to 160 feet |
HD 5000 | 5 x 5 inches | 400 – 1800 | up to 225 feet |
HD 5000 | 6 x 5 inches | 400 – 1800 | up to 225 feet |
HD 6000 | 8 x 6 inches | 450 – 2500 | up to 200 feet |
HD 8000 | 10 x 8 inches | 1400 – 3600 | up to 230 feet |
HDX 10000 | 12 x 10 inches | 1600 – 5000 | up to 240 feet |
HD 12000 | 14 x 12 inches | 2600 – 7300 | up to 180 feet |
The Benefits of Managing Slurries and Complicated Liquids for Industry
01
Self-Priming Capability
Self-priming can refer to a pump that is capable of handling the fluid suction without requiring extra components to ensure that it draws the fluid from a distant source or point in the system. This feature allows for simple processes of assembly as well as doing away with additional priming procedures.
02
Long-Lasting Durability
All of the commonly used seals, such as o-rings, mechanical seals, and liners, are implemented with state-of-the-art pump liners for successively handling the properties of tough fluids, whether chemically or physically erosive or abrasive in nature. This makes it possible for the identified materials and their components to offer better performance by enduring even more severe conditions in order to deliver better results.
03
Wide Range of Applications
The application of submersible suction pumps is rather broad and the equipment is capable of pumping various kinds of liquids – from those containing a lot of solids in solution, sludge, etc. Because of its diverse use some of the areas that require the products include mining, construction, industrial processes and water treatment industries.
04
Lower Maintenance Needs
The general framework on which these pumps are constructed is a rigid structure complemented by an effective working mechanism. This strong construction also means that the rotary scrubber will require less maintenance often, and therefore will have less time out of order and a lower maintenance cost.
05
Consistent Operation
The flooded suction design also guarantees that the pump always has an adequate supply of fluid to draw and eliminates any possibility of vibration from the lack of fluid as a base.
Related Equipment
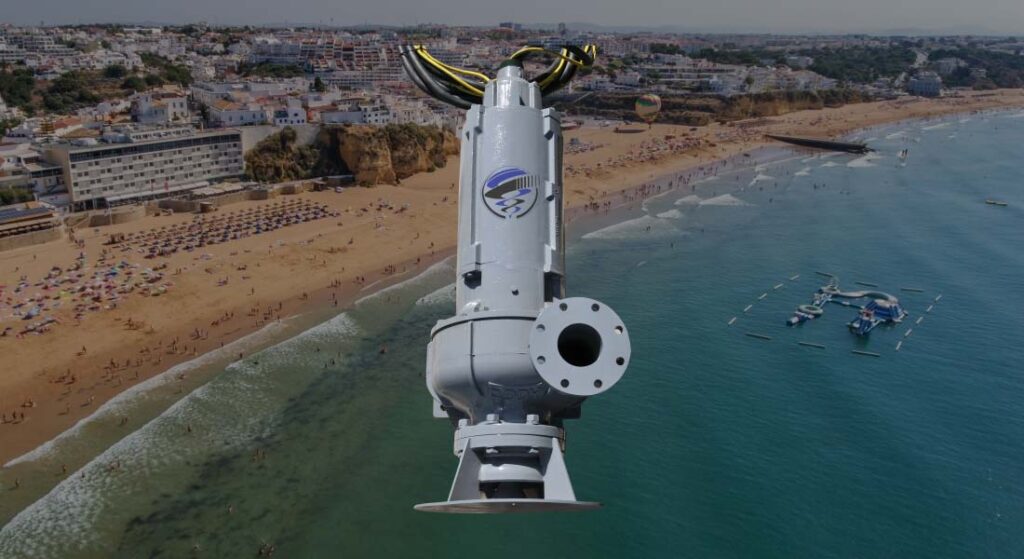
Submersible Slurry Pumps
These are the pumps that are installed and positioned right into the liquid being moved; they offer no need for priming as the pumping system is always submerged. They also take less time to install and operate, which in turn increases the efficiency of the pumping system.
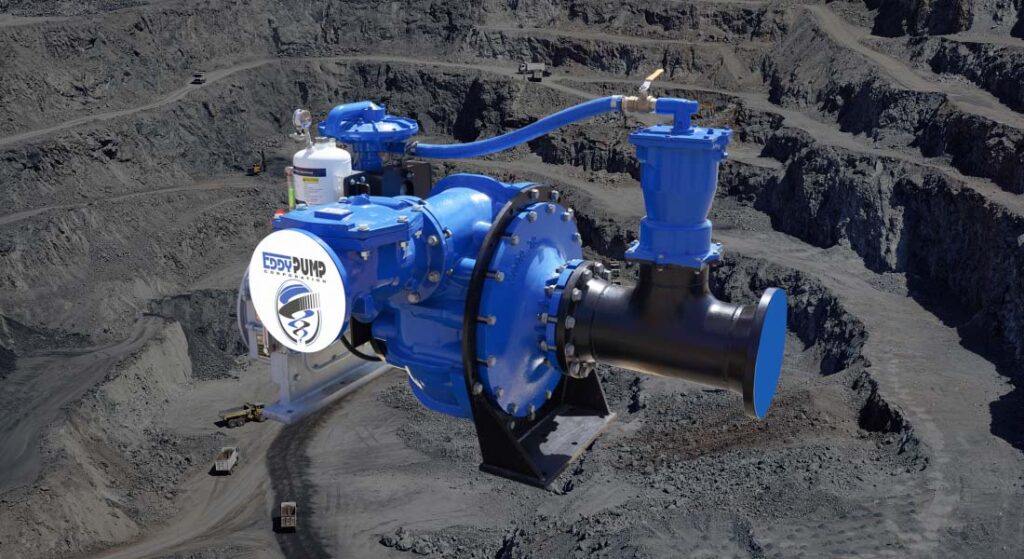
Self-Priming Pumps
Standing on the water, these units have a suction hose that filters mud in a manner similar to an oversized vacuum cleaner. One of the main advantages of their use is that the tools are portable, thus suited to numerous uses.